Can You DIY Spray Foam Insulation? A Homeowner’s Guide to Success, Safety, and Savings
Introduction: Is DIY Spray Foam Insulation Right for You?
Spray foam insulation is renowned for its ability to dramatically improve a home’s energy efficiency by sealing air leaks and increasing comfort. Many homeowners wonder if they can apply spray foam insulation themselves and whether it’s a worthwhile DIY project. By understanding the benefits, challenges, key steps, safety requirements, and cost comparisons, you can confidently decide if DIY spray foam insulation is suitable for your needs.
Understanding Spray Foam Insulation: Benefits and Limitations
Spray foam insulation comes in two main types: open-cell and closed-cell . Both create an air seal that can outperform traditional materials like fiberglass or cellulose, but they differ in cost, rigidity, and R-value (a measure of insulation effectiveness). Closed-cell foam offers the highest R-value and acts as a vapor barrier, while open-cell foam is more flexible and generally less expensive.
The primary benefits of spray foam insulation include:
- Superior air sealing : Reduces drafts and energy loss by filling gaps and cracks with an expanding foam.
- High R-value : Delivers greater insulating power per inch than many other insulation types [4] .
- Moisture and vapor barriers : Particularly with closed-cell foam, helping to prevent mold and mildew.
- Long-term savings : Lower heating and cooling bills by reducing energy waste [2] .
However, spray foam may not be ideal for every project. Large or inaccessible areas, concerns about chemical exposure, or local building code restrictions may require professional installation. Always check your municipality’s building codes before starting a DIY insulation project.
Should You DIY or Hire a Professional?
DIY spray foam insulation is feasible for many small to medium-sized projects, such as sealing gaps in basements, attics, or around windows and doors. Homeowners may save hundreds or even thousands of dollars by taking on the work themselves. For example, one DIYer insulated an attic with spray foam kits and foam board for approximately $2,000, compared to a $5,000+ professional quote [5] . However, professional installers are recommended for large areas, complex structures, or where code compliance and warranty coverage are critical.
When deciding, consider:
- Project size : Small gaps and localized areas are suitable for DIY; whole homes or large attics often require pros.
- Skill and comfort level : DIY requires careful prep, protective equipment, and attention to detail.
- Budget : Kits typically cost $300-$1,500, while professional jobs can range from $2,000 to $10,000 or more, depending on size and complexity [3] .
- Health and safety : Proper handling of chemicals and good ventilation are essential.
Step-by-Step: How to Apply Spray Foam Insulation Yourself
Follow these detailed steps for a successful DIY spray foam insulation project:

Source: asia-can.com
1. Preparation and Safety
Preparation is key. Wear gloves, safety goggles, and a respirator to protect against fumes and skin contact. Ventilate the area well and keep all sources of ignition away-the chemicals are flammable [2] . Read all manufacturer instructions thoroughly before beginning application [1] .
Ensure the area to be insulated is clean, dry, and free of dust or debris. Seal larger gaps (over a quarter inch) with caulk or a suitable sealant before applying foam. Cover floors and nearby surfaces with drop cloths or newspaper to catch any overspray.
2. Locating Air Leaks
Common areas for air leaks include:
- Door and window frames
- Baseboards and electrical outlets
- Pipes, wires, and conduits passing through walls
- Attic hatches, basement rim joists, and crawl spaces
Inspect these areas carefully and mark places that need sealing. For hidden leaks, consider using an infrared thermometer or smoke pencil to identify drafts.
3. Choosing the Right Spray Foam Kit
Spray foam insulation kits are available at major home improvement retailers and online. Kits are typically rated by “board feet” (one square foot at one inch thick). For example, a 200 board foot kit will cover 200 square feet at 1-inch depth, or 100 square feet at 2 inches [3] . Calculate your project’s needs and purchase accordingly. For larger projects, multiple kits may be necessary.
4. Application Technique
Start by practicing on a scrap piece or waste area to gain control of the foam. Hold the nozzle 6-18 inches from the surface and apply the foam in a steady, continuous bead. Fill gaps no more than halfway, as the foam will expand to fill the remaining space [2] . Mist the area lightly with water before and after application to help the foam cure faster if recommended by the manufacturer.
Apply foam in layers, allowing each to cure before adding more. This ensures better results and avoids overfilling. After curing, trim any excess foam with a serrated knife for a neat finish.
5. Finishing Touches and Cleanup
Once the foam is fully cured and trimmed, fill any remaining small gaps with caulk. Dispose of empty spray foam canisters according to local hazardous waste guidelines. Store leftover materials safely, away from heat and children.
Cost Comparison: DIY Versus Professional Installation
DIY spray foam insulation offers significant savings over hiring a contractor, especially for small or medium projects. A typical DIYer spent around $2,000 on kits and foam board to insulate an attic, whereas professional services quoted $5,000 or more for the same job [5] . For smaller tasks (sealing gaps and cracks), a single kit costing under $500 may suffice.
However, professionals have access to high-output equipment and may offer warranties or guarantees on their work. For complex or large-scale jobs, professional services may provide better long-term value despite the higher upfront cost.
Expert Tips for Successful DIY Spray Foam Insulation
Success with DIY insulation depends on preparation, technique, and safety. Keep these expert tips in mind:
- Always wear appropriate protective equipment, including gloves, goggles, and a respirator.
- Work in a well-ventilated area and avoid open flames or sparks.
- Follow kit instructions exactly, including recommended temperature ranges for application and curing [1] .
- Use a drop cloth or plastic sheeting to protect floors and nearby surfaces [2] .
- Apply foam in thinner layers to ensure thorough curing and avoid trapped moisture.
- Trim cured foam for a clean finish and inspect for any missed gaps or cracks.
Common Challenges and How to Overcome Them
DIY spray foam insulation is not without its challenges. Homeowners may encounter:
- Running out of foam : Measure your area carefully and buy extra to account for waste. A 200 board foot kit covers 200 square feet at 1-inch thick [3] .
- Messy application : Practice first and work slowly. Overspray can be difficult to clean.
- Improper curing : Ensure correct temperature and humidity. Some kits require preheating tanks for best results.
- Missed spots or uneven coverage : Inspect when finished and touch up as needed.
- Chemical exposure : Use all recommended safety gear and ventilate well.
For those who are uncomfortable with chemicals, have large or complex projects, or need guaranteed results, hiring a professional is a viable alternative.

Source: britannica.com
Alternative Approaches: Other Insulation Methods
If spray foam seems daunting or is not suitable for your application, consider these alternatives:
- Fiberglass batts or rolls : Straightforward to install and widely available, though they may not seal air leaks as effectively.
- Blown-in cellulose : Good for attics and wall cavities; can be a DIY project with rental equipment.
- Foam board : Provides high R-value and is easy to cut to size for specific applications.
Each insulation type has unique strengths and may be used in combination for best results.
How to Access DIY Spray Foam Insulation Kits and Resources
Spray foam insulation kits are available at major home improvement stores such as Lowe’s, The Home Depot, and Menards. You can visit these retailers in person or search their official websites for “spray foam insulation kits” to find options that fit your needs. Always compare products, read reviews, and ensure compatibility with your project.
For specific guidance or finding local professionals, you can contact your local building supply store or search for “insulation contractors near me” using reputable online directories. For building codes and safety requirements, consult your city or county’s official building department website.
Summary: Key Takeaways and Next Steps
DIY spray foam insulation can be a cost-effective way to improve comfort and reduce energy bills when approached with preparation, safety, and the right tools. Carefully assess the scale of your project and your comfort with chemicals before starting. If in doubt, consult a professional or start with a small area to build experience. For further information, consider visiting established home improvement retailers or seeking advice from certified energy auditors.
References
- [1] VB Insulation (2024). DIY Foam Insulation: Step by Step Guide for Home Projects.
- [2] Lowe’s (2024). How to Apply DIY Spray Foam Insulation.
- [3] YouTube (2025). DIY Spray Foam Insulation VS. Pros – Was it worth it?
- [4] Kraken Bond (2023). Save on Energy Bills with DIY Spray Foam Thermal Insulation.
- [5] YouTube (2024). DIY Spray Foam Insulation: How I Insulated My Attic and …
MORE FROM 9scholarships.de
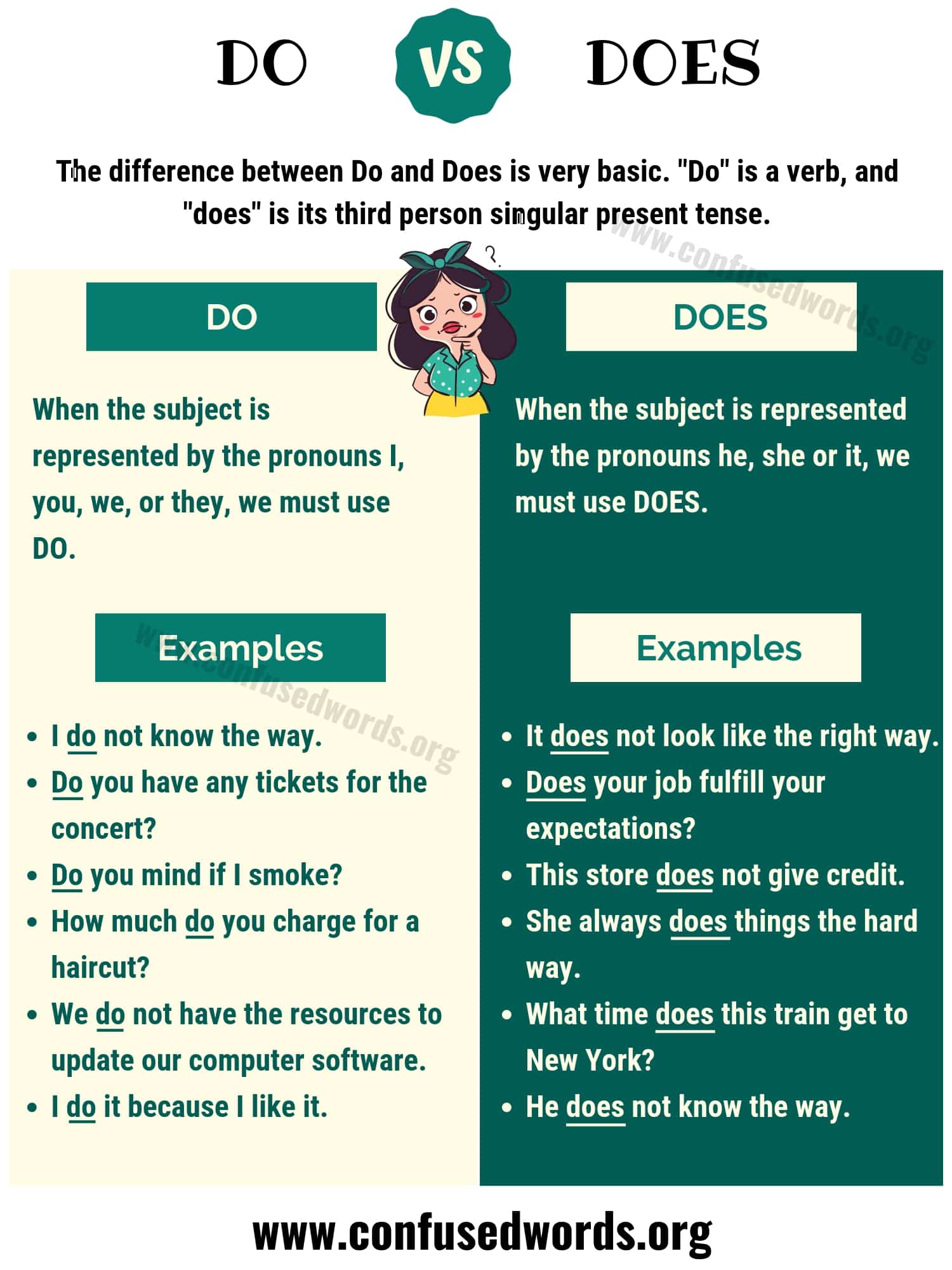
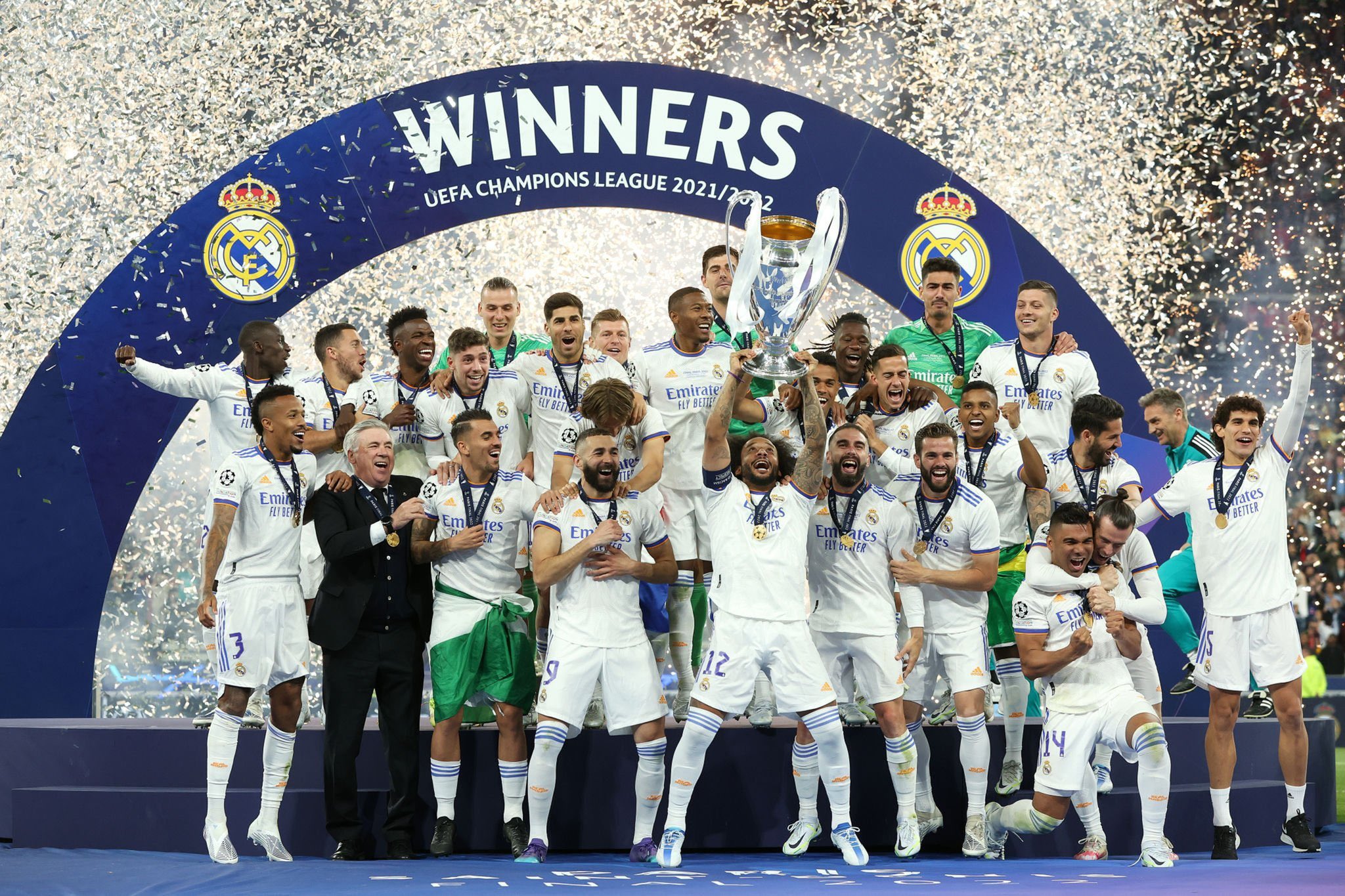
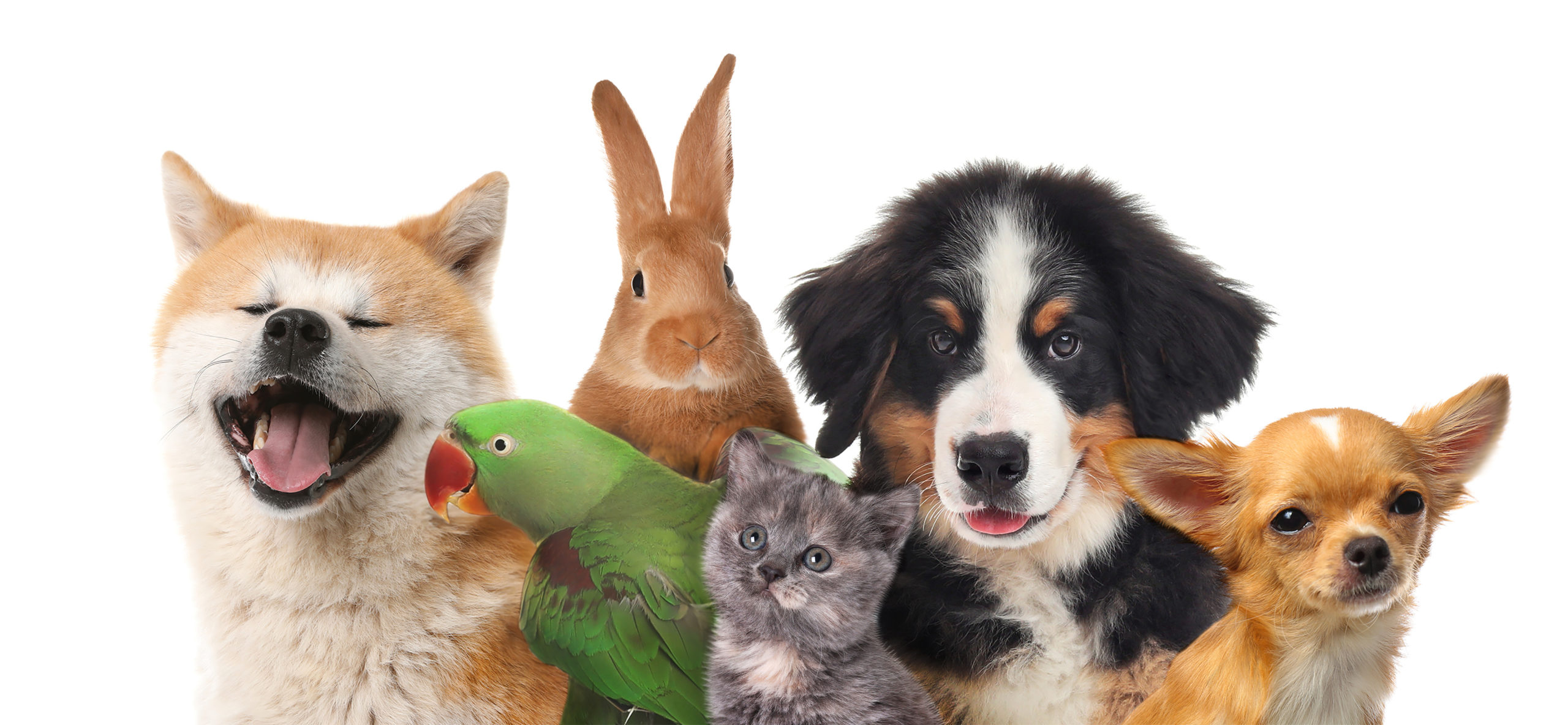
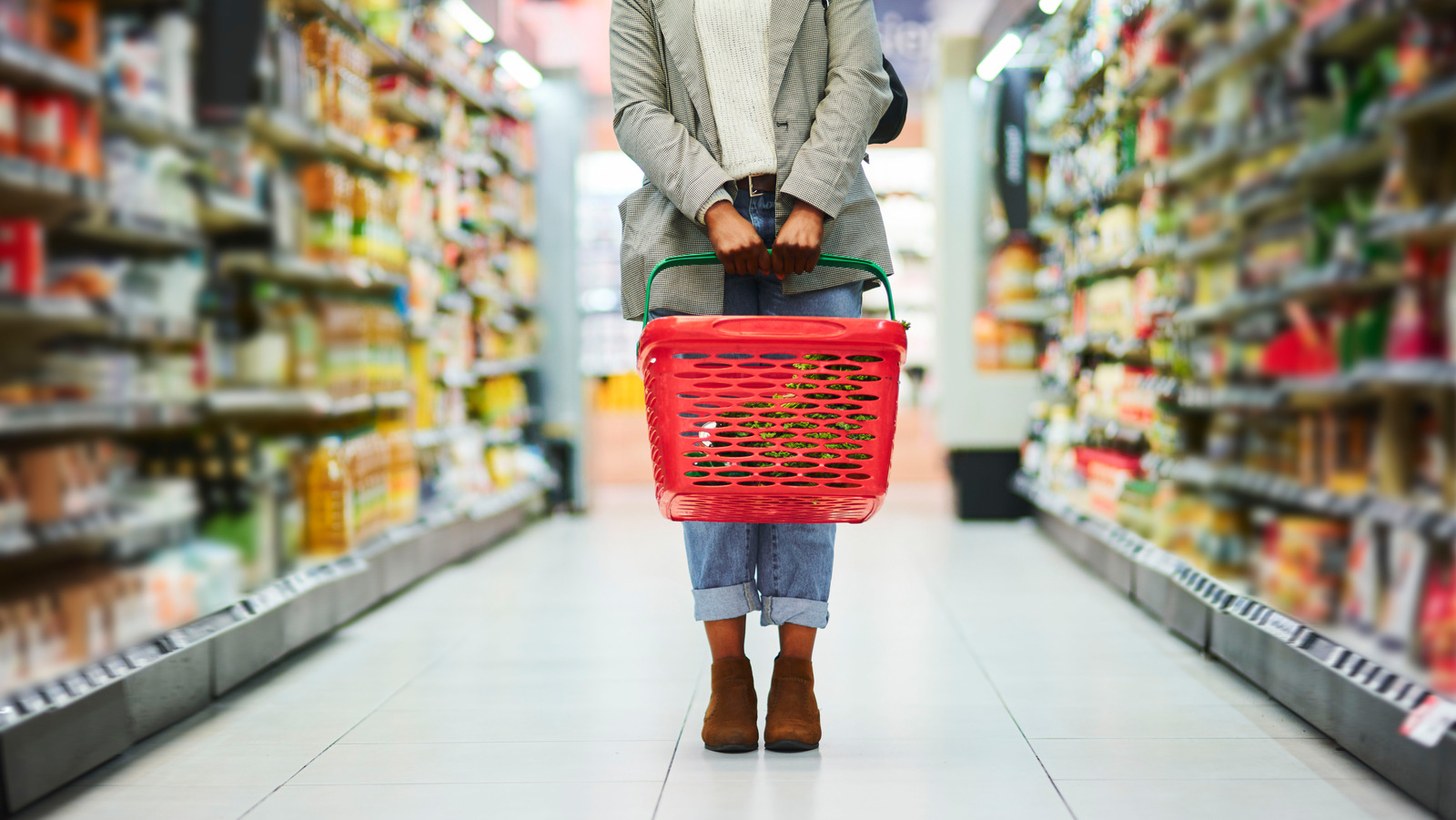
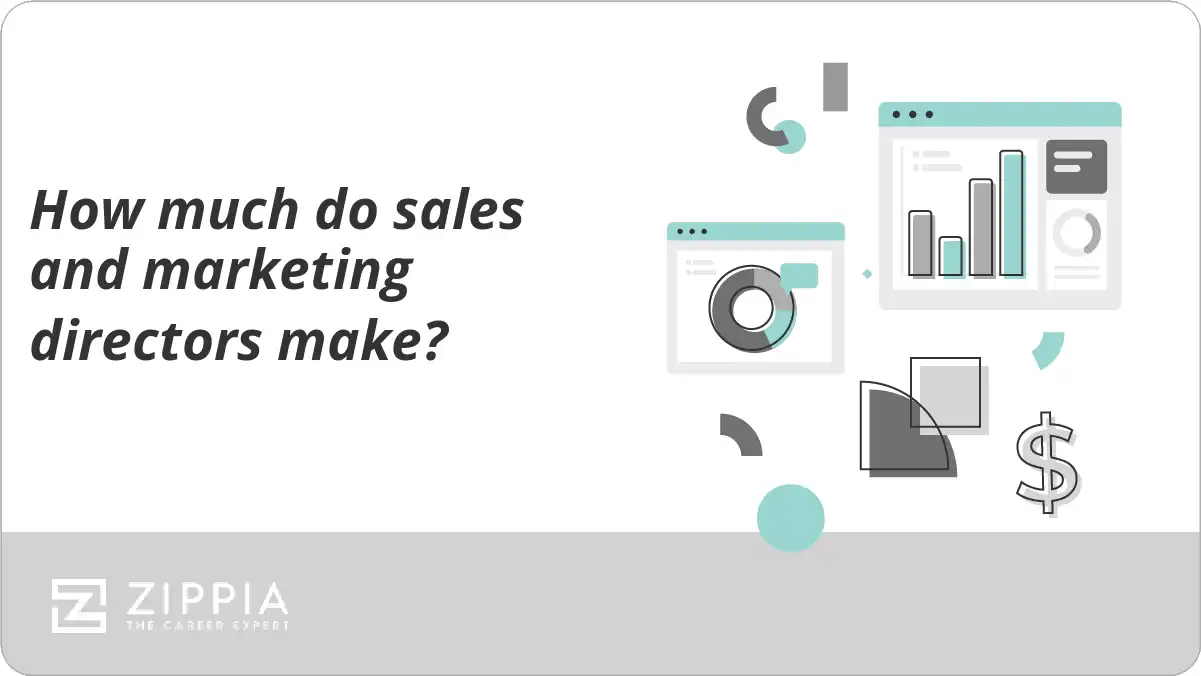
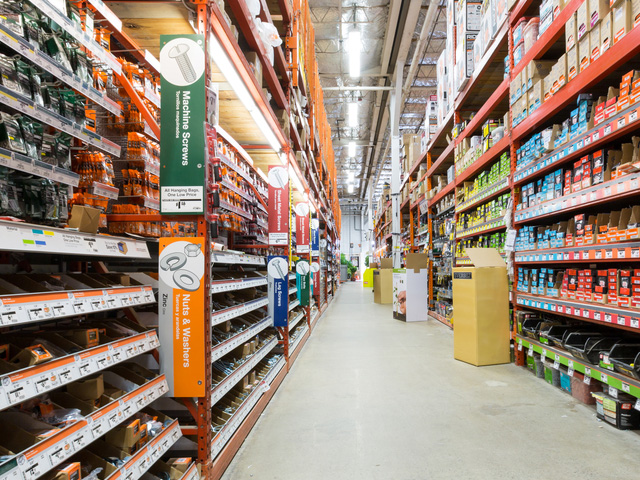
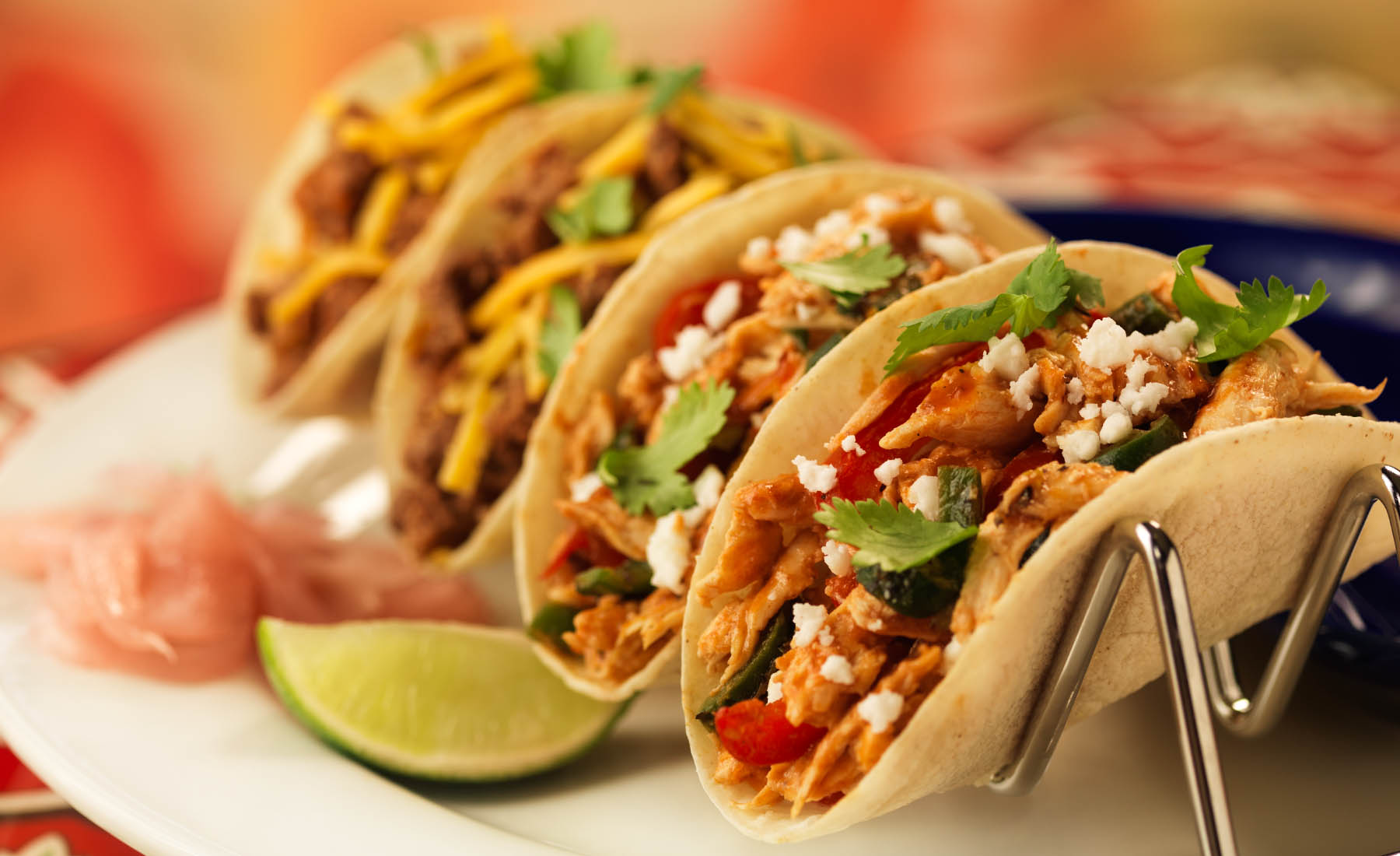
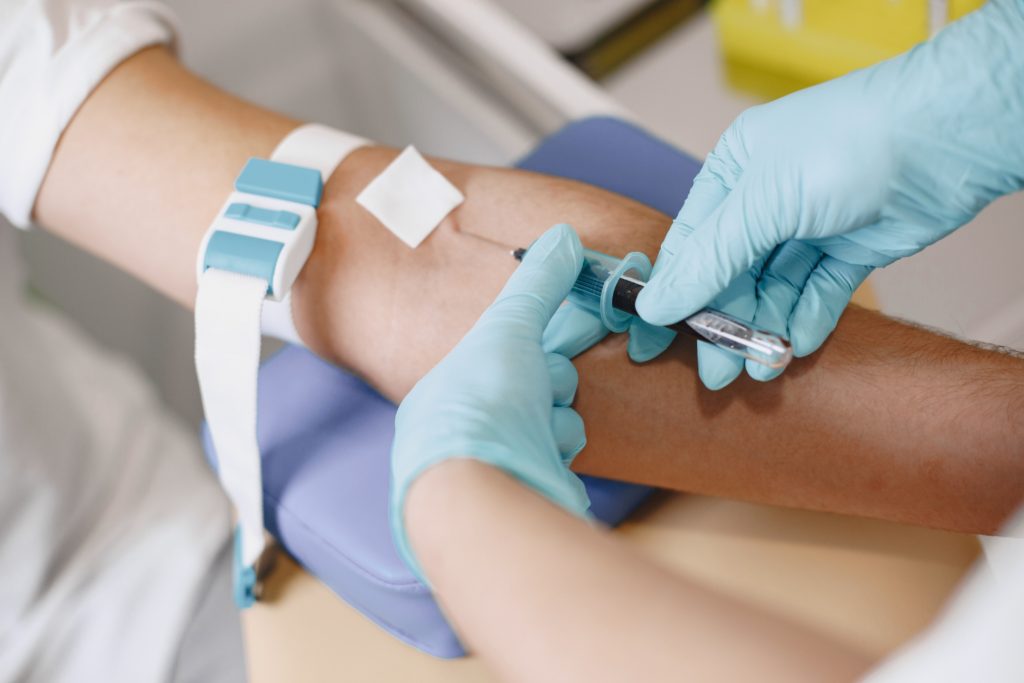
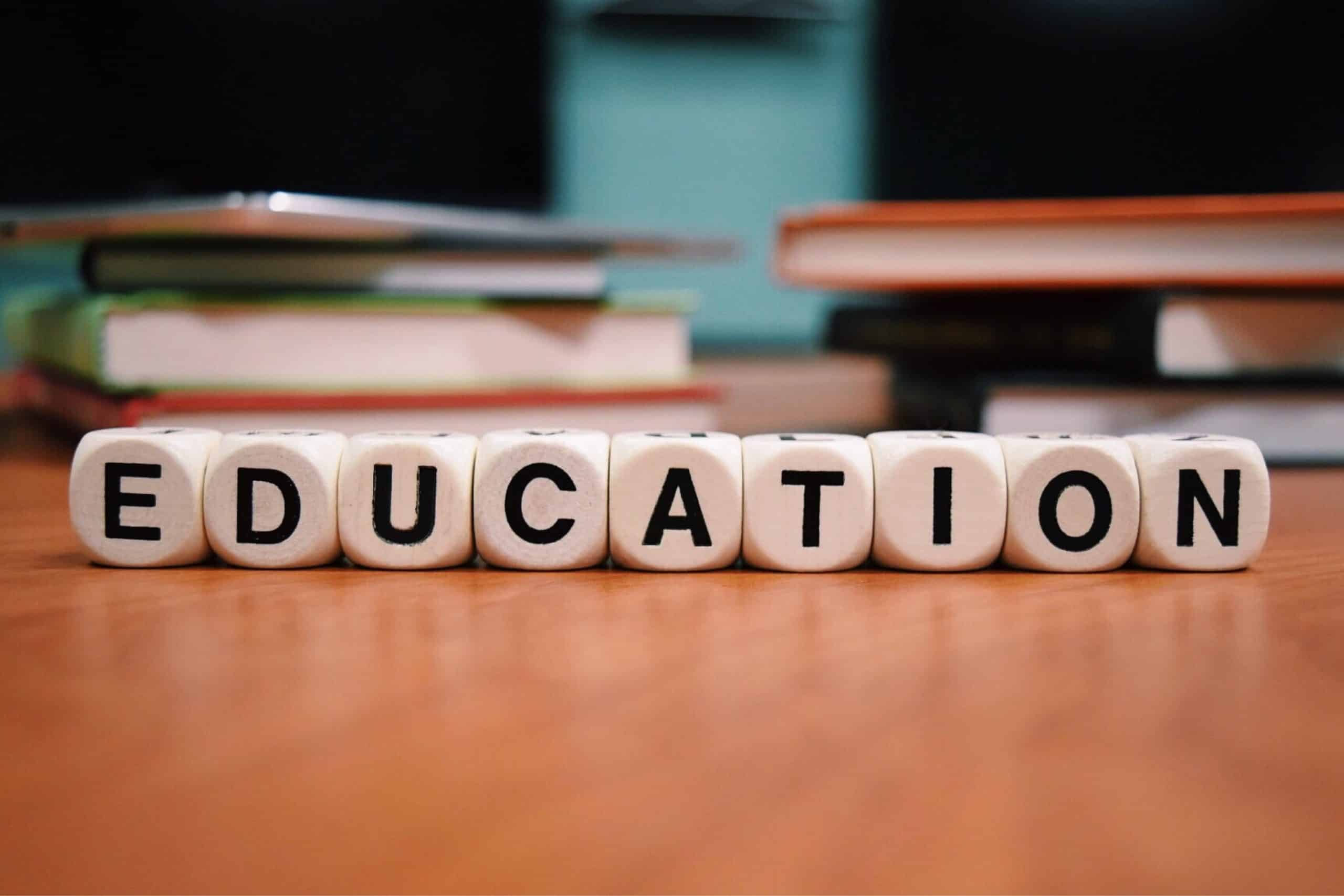
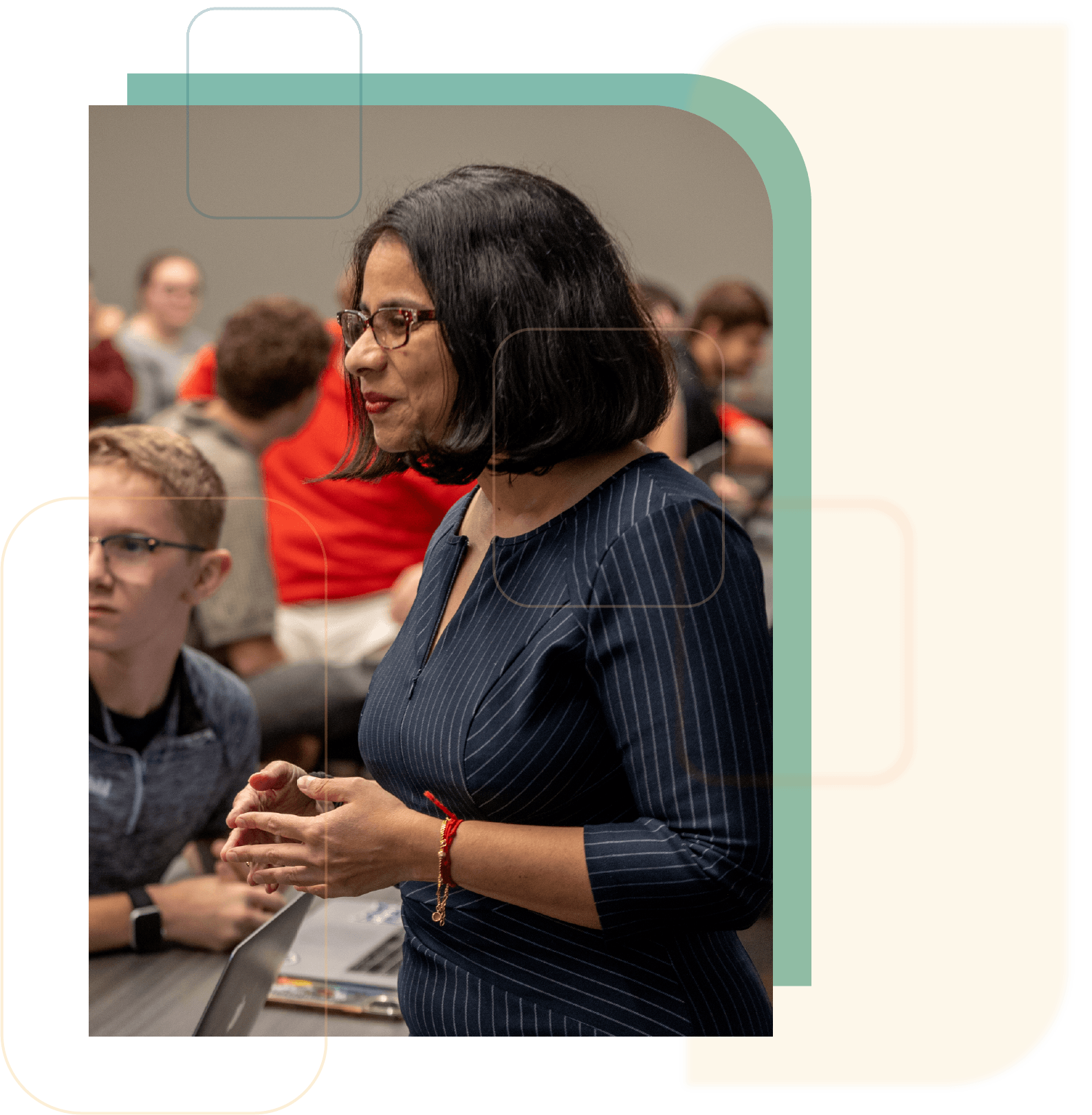
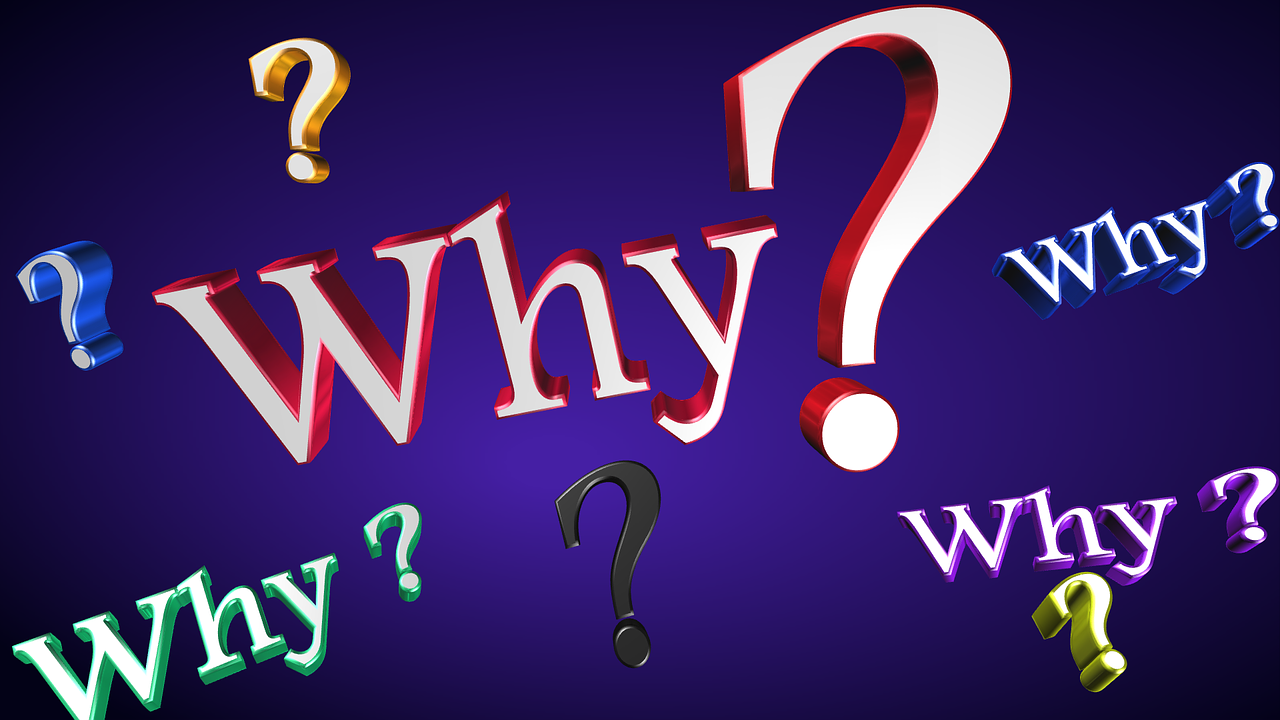
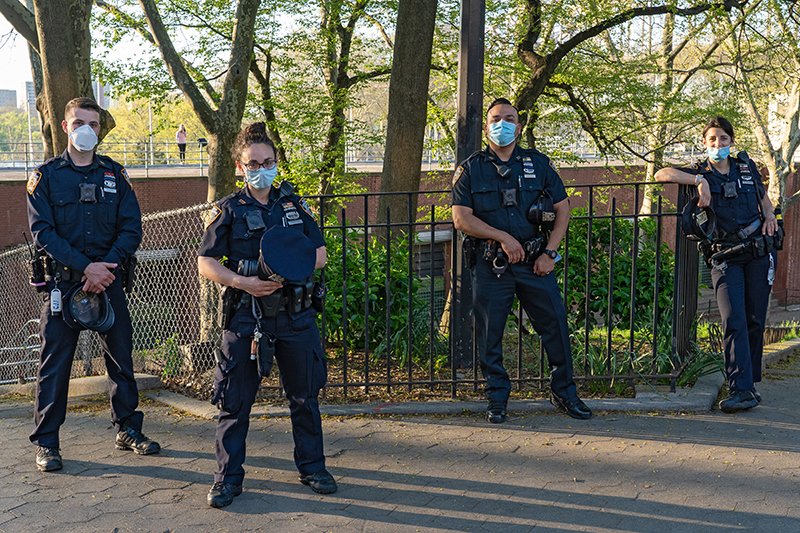